Opportunities and the future of Indian Paper industry in the next decade
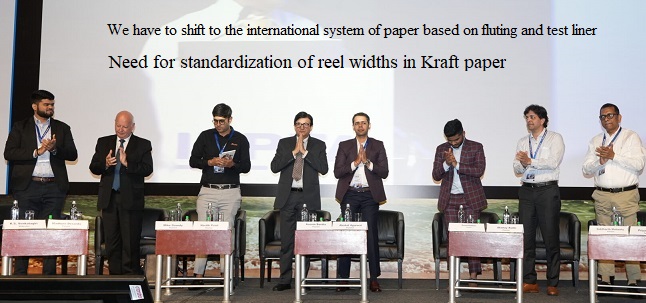
Opportunities and the future of Indian Paper Industry in the next decade
- Many mills have come up in the Kraft paper segment with capacities of up to 600 to 700 tons per day
- We have to shift to the international system of paper based on fluting and test liner.
- We need to find a way to infuse some long fiber into our paper, maybe by using more virgin pulp or other wood substitutes like straw or Bagass
- Every year, 500 billion plastic cups and 260 billion paper cups with plastic laminate are made, and of the laminated paper cups, less than one percent are recycled.
The Pulp and Paper Times | March 2023
The panel discusses the opportunities and the future of the Indian Paper industry in the next decade at IPPTA’s AGM held at Hyderabad. Panelists share their views and put forward opinions on what challenges the Indian paper industry currently faces and how the industry can solve them using different mediums.
Sharing his views on the growth of the trades and paper industry in the next decade throughout Asia, Mr. Mike Grundy, CEO of Amazon Papyrus Chemicals Private Limited, said, “My perspective is a bit outside of India. As our company operates throughout Asia, I have a view from there. Firstly, we have all heard about Environmental, Social, and Governance (ESG), and our company was not focused on it until about two or three years ago when reality struck. As a chemical company, we had to take it seriously, and found that customers look at our ESG credentials. If they want us to be a supplier, then we have to meet their standards. If anyone thinks that ESG is just a box-ticking exercise, I assure you it is not. Big brands and companies make statements and accounts their sustainability goals in their statements, and share how to achieve those goals. Sometimes there is a cost involved, but most of our actions have given us a return on investment.”
“Moving away from single-use plastic is a huge opportunity for the pulp and paper industry. Currently, around 40% of all packaging is plastic-based, and around 30% is paper- or fiber-based. That will change rapidly in favor of the paper industry, giving an opportunity and challenge to everyone. Every year, 500 billion plastic cups and 260 billion paper cups with plastic laminate are made, and of the laminated paper cups, less than one percent are recycled,” he added.
Answering a question about growth and how to achieve it, Mr. Siddharta Mohanty, Vice President & Unit Head of ITC PSPD Bhadrachalam Unit, said, “When we discuss growth, it has to be profitable. In India, there are two types of growth: one is investment-based, and the other is consumption-based. In India the growth is based on consumption and we need to figure out how to improve consumption. There is no competition because there is no investment-based growth. Before moving ahead with cost competitiveness, the first thing is to prepare a raw material strategy. There are three different types of raw materials: waste paper; the industry has to work out a strategy for waste paper collection because that is the major input cost. Second is wood; the industry needs to work with farmers, which has to be a win-win for both the farmer and society. The third is agricultural residue, which we need to oversee. It is going to impact us, so we have to start monitoring the agricultural terrain and develop strategy accordingly.”
He added, “The second is technology; we have to continuously upgrade the technology to be at par with the quality of international standards. Technology comes with investment, and it is a capital-intensive industry. Third is digital technology; today, artificial intelligence and machine learning (AIML) are largely adopted in different industries to optimize operating parameters and performance. It reduces consumption and increases output.”
Mr. Akshat Agarwal, Director of Vijay Anand Kraft Paper Private Limited, shared his thoughts on how paper mills can adapt to the changing demands and how they can use this as an opportunity to grow their market for finished products. He said, “In the last 2-3 years, many mills have come up in the Kraft paper segment with capacities of up to 600 to 700 tons per day, calling for standardization of the products. Instead of making paper based on BF, we have to shift to the international system of paper based on fluting and test liner, correlating with the board properties. There is a need for standardization of reel widths in Kraft paper. Currently, we sell paper with reel widths with a difference of one centimeter, so that needs to be changed, and a more standard system needs to be followed. It will help the mills improve their efficiency and compete in the international market.”
He added, “Under the Make in India initiative, the companies set up their plants in India, and sell their products overseas. In India, there are concerns regarding foul smell being generated from the Kraft paper mills. The issue arises due to poor ETP designs and the Zero Liquid Discharge (ZLD) permissions that they had from their PCBs. Recently, steps have been taken on how technology can be used to eliminate the bad odor in ZLD plants, and I am sure we will find some solutions.”
“One of the factors to control is the amount of long fiber present in our finished product. Most mills in India are recycled-based, and even the material or recovered fiber imported from the USA and Europe become weak, or the amount of long fiber is reducing due to recycling. We need to find a way to infuse some long fiber into our paper, maybe by using more virgin pulp or other wood substitutes like straw or Bagass, and maybe some technologies, which can improve the tear or act as a substitute for the long fiber, might help,” he added.
He said, “What is amazing is how new markets are opening up, like how micro flutes started gaining importance and are competing with mono cartons. The E and F flutes are finding applications in cosmetics, confectionaries, household chemicals, Etc. So this is because of the excellent printing capabilities. The sector requires a low GSM and a smooth finish, so the white test liners are finding applications. Another application is barrier-coated papers. We have seen a lot of seafood, fruits, and vegetable trays; sugar and flour packaging that is exported, and the contents need to be protected from external moisture, so the barrier-coated paper has a huge potential and demand.”
Mr. Akshay Rathi, Director of Kaygaon Paper Mills Private Limited, shared, “There are immense opportunities for the packaging sector to grow sustainably. In India, the per capita paper consumption is around 15 kg, which is likely to grow to over 30 kg in the next few years, whereas the global average is close to 60 kg. These numbers itself shows the scope for the Indian paper industry. Domestic consumption will help to achieve the growth, and objective of GoI to become a 5 trillion-dollar economy through exports. Currently, India stands at three trillion dollars, we see an opportunity coming our way in the next few years. The global supply chain is getting more integrated, and there are immense opportunities as the manufacturing base shifting to India.”
“As far as exports are concerned, we have seen that packaging paper can be exported. The exports of floating medium and test liner touched over 2 lakh tons per month during pandemic, and it continued for several months. However, the exports could not sustain themselves for various reasons, and issues like bad odor, logistics, run ability, and quality, so if we work on these aspects, there is a huge opportunity for the packaging industry. India exports to the Far East, the Middle East, Latin America, and African countries, these exports that happened were more out of compulsion than out of choice, because China shifted its policy on raw material imports, so for us to sustain these exports, we need to work on quality, and one cannot emphasize enough odor elimination.”
He shared, “For a ton of paper, the recycle-based paper mills consume less than 300 kWh power and less than 2-meter cube water. The segment has achieved these numbers, and it is not easy to digest. There are other areas where a lot can be done to save energy, like installation of rooftop solar plants and using biomass as fuel. Under Swachh Bharat Mission, more emphasis is given on garbage collection and its processing, not only within corporation limits, but also at the gram panchayat level. The processed can be used to convert waste into energy, and I think some government initiatives are promoting and funding local gram panchayats and corporations to collect more waste.”
Mr. Hardik Patel, Director of Sales and Marketing, Om Sree Papertek (P) Limited, shared, “The mid and small-level industries can achieve the targeted sustained growth. However, one of the problems is giving stability to customers. Today, due to the deficiency of fiber, we have waste paper people holding us hostage, and we have to rely on local procurement, which is an unorganized sector. The imported fiber that comes has a lead time of around 60 or 90 days, during which waste paper collectors hold us, hostage, by not supplying or by increasing the prices, and in turn, we fail to provide a sustained and stable market creating uncertainty for the end customer.”
Mr. Madhure Desarda, Director of Operations, Parason Machinery (India) Private Limited, sharing how to achieve growth, said, “I would talk about three categories: How we can have growth in the next decade, how to sustain, and how AIML will play a role in the future. India has more than 600 to 650 paper mills, and the average mill size for small, medium, and large would be around 150, 200, or up to 300 tons a day. Today, India has 60 molded fiber plants; the average size of the plant is 3–4 tons a day, so if you multiply 60 by 4, it is 240 tons per day, whereas, in China, the average plant for molded fiber is 250 tons a day. This molded fiber industry is made for China and India because it is a bit labor- and capital-intensive and we need good fibers, so I believe India has a good future.”
He added, “This industry will be worth around 5 billion dollars in the next one to two years, so I believe this will be a good opportunity for us to enter it, not only on the molded fiber production side, but also on the pulp supply side. Another 50–60 plants are coming into India, so any big mill, whether we go for Bagass pulp, wheat straw, or bamboo pulp, will be a good addition to the industry. Regarding sustainability, we need youth or new people in the industry. Educational institutions should be encouraged to start paper engineering courses. It can start with the elective courses in the last year and with the optional practical training, so there is an infusion of fresh blood in the paper industry, and we can have the right talent.”
Web Title: Opportunities and the future of the Indian Paper industry in the next decade